Boost Your Production Quality with State-of-the-Art Metal Stamping Solutions
Enhancing Performance and High Quality With Modern Metal Stamping Techniques
As the demands for accuracy and efficiency proceed to rise, the combination of automation and digital tools into the steel marking process has become paramount. By exploring the complex interplay between modern technology, automation, and accuracy in steel stamping, a path in the direction of unrivaled performance and top quality guarantee unfolds.
Benefits of Modern Metal Marking
Modern metal marking deals countless benefits in terms of performance, precision, and cost-effectiveness in the manufacturing sector. One of the vital advantages of modern steel stamping is its capacity to successfully generate high volumes of complex steel parts with consistent high quality. This process gets rid of the demand for numerous operations as it can do numerous tasks such as blanking, piercing, forming, and reeling in a single procedure.
Moreover, modern-day steel stamping makes it possible for makers to achieve tight resistances and precise specs, ensuring that each component fulfills the needed standards. This high degree of precision leads to very little material waste, lowered rework, and general better item high quality.
In addition, modern-day metal marking is a cost-effective production approach. In essence, contemporary steel marking offers a competitive edge to makers looking to improve performance and top quality in their procedures.
Advanced Technologies in Metal Stamping
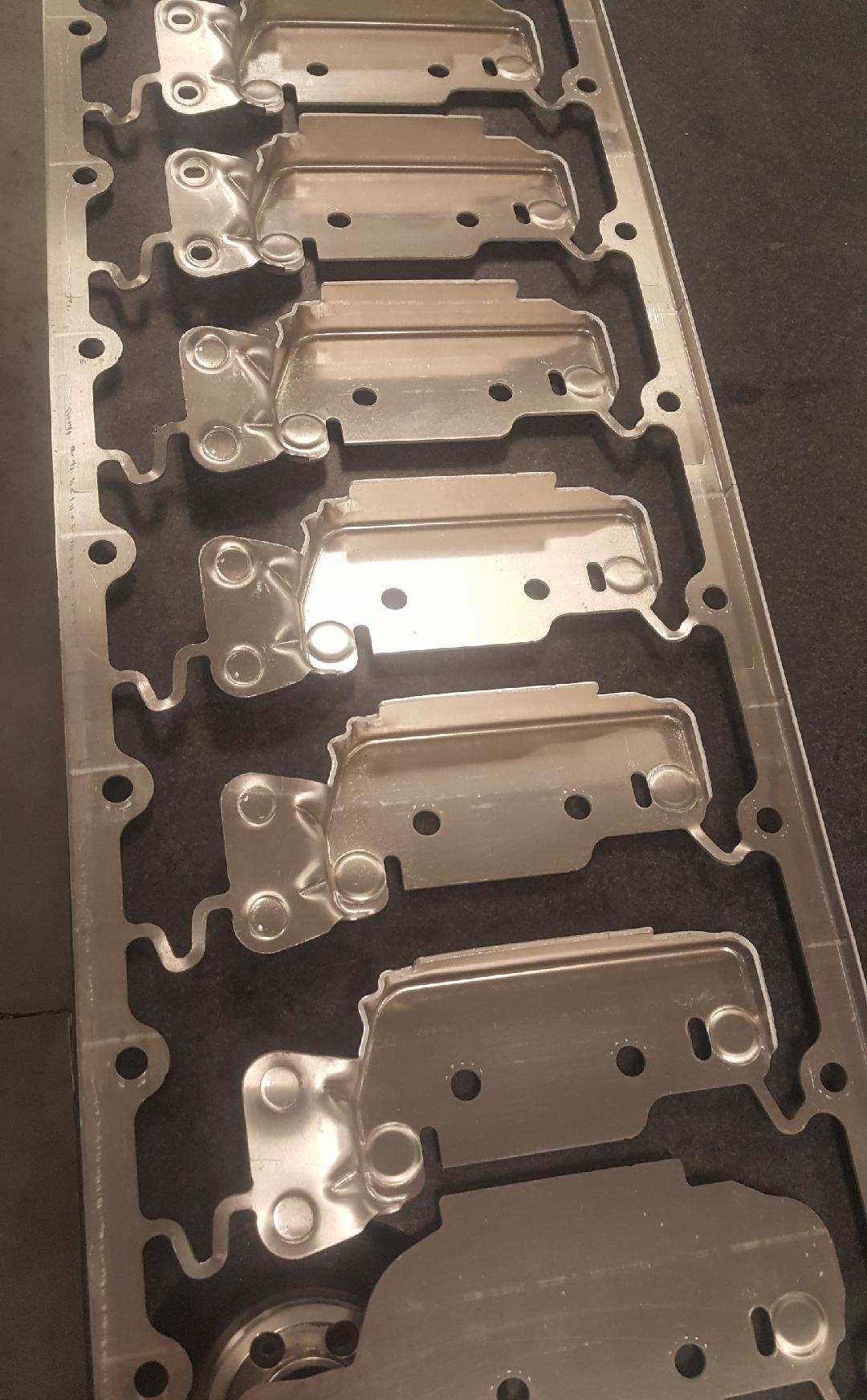
Another key innovation changing metal stamping is the use of servo presses. Unlike typical mechanical presses, servo presses use higher control over the rate and pressure applied throughout the stamping process. This control not only boosts the quality of the stamped components but likewise minimizes material waste and energy consumption.
In addition, innovations in simulation software application have actually allowed makers to practically test and enhance the stamping process prior to physical production starts. This online prototyping aids determine possible problems early on, causing cost financial savings and faster time-to-market for brand-new items. Generally, these advanced modern technologies in steel stamping are driving unmatched levels of productivity and high quality in the market.
Improving Effectiveness Via Automation
The combination of automated systems has considerably enhanced the effectiveness of metal marking procedures. Automation in steel marking operations uses a myriad of advantages, including increased manufacturing prices, enhanced accuracy, and lowered labor costs. By making use of robotic arms and computer-controlled equipment, jobs that were previously lengthy and susceptible to errors can currently be carried out swiftly and with amazing accuracy.
Automated systems have the capability to deal with recurring jobs with uniformity, causing greater efficiency degrees and lowered cycle times. This enhanced effectiveness not only results in cost savings but also makes sure a much more streamlined and dependable production procedure. go to the website Furthermore, automation permits real-time tracking and data collection, making it possible for suppliers to identify and deal with problems without delay, further enhancing the general effectiveness of metal stamping operations.
Additionally, automation advertises a much safer working atmosphere by lowering the requirement for hands-on treatment in harmful jobs. By handing over these responsibilities to automated systems, employees can concentrate on more facility and value-added activities, adding to a much more efficient and efficient workflow in the steel stamping market.
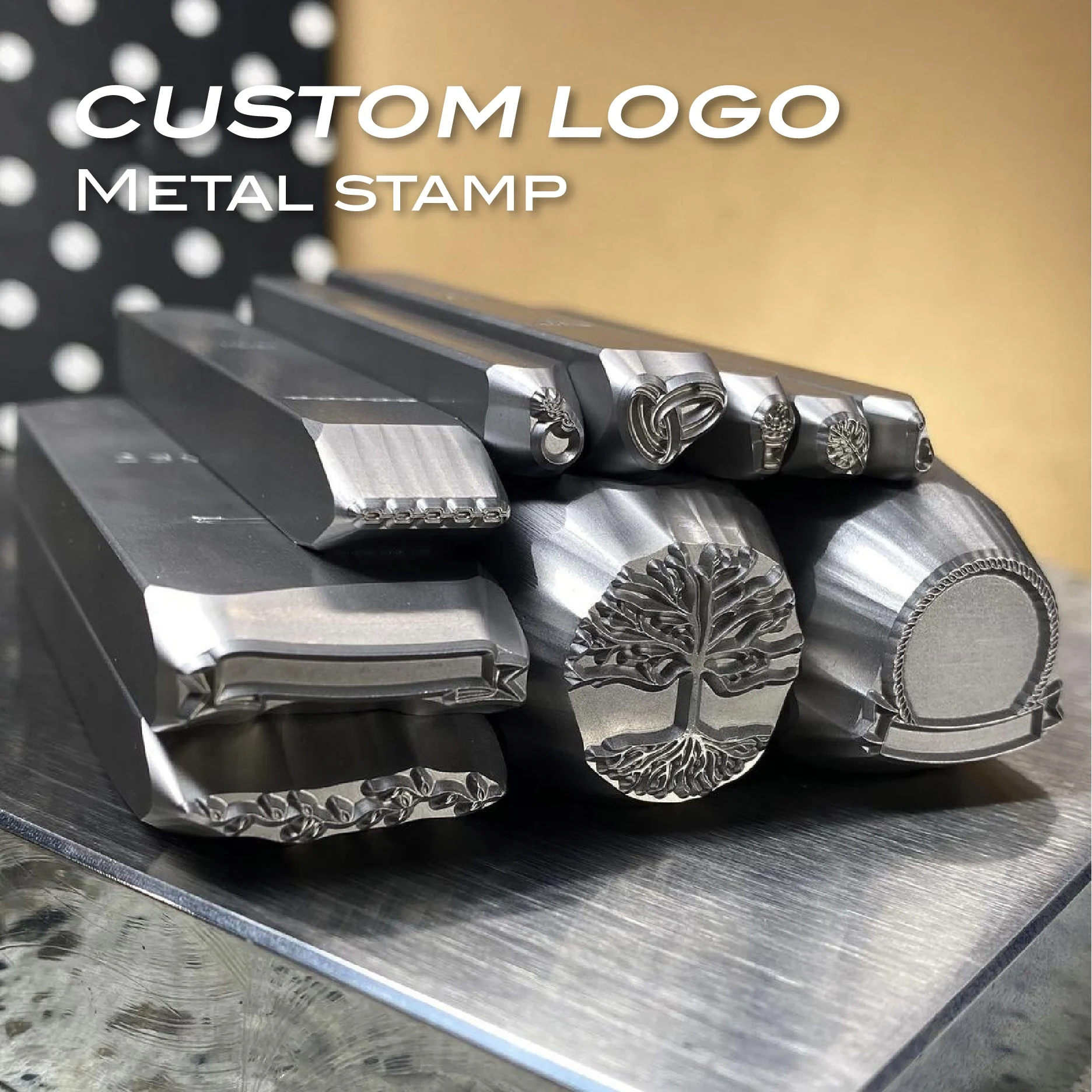
Quality Assurance Actions in Stamping
Implementing rigid quality assurance actions is vital in ensuring the precision and uniformity of metal marking procedures. By developing robust quality assurance procedures, producers can recognize and rectify any kind of discrepancies or defects in the stamped parts, inevitably enhancing item high quality and client complete satisfaction. Among the primary quality assurance steps in metal marking is conducting routine examinations throughout the manufacturing cycle. These inspections entail checking helpful site the measurements, surface area coating, and total stability of the stamped parts to validate compliance with the given needs.
Furthermore, carrying out sophisticated technologies such as automated vision systems can further improve the quality assurance procedure by making it possible for real-time surveillance and discovery of any kind of anomalies throughout manufacturing. These systems utilize cameras and computer system formulas to examine parts with high precision and precision, reducing the threat of problems running away into the end product.
Furthermore, establishing an extensive documentation system that videotapes quality assurance data and assessment outcomes is important for tracking efficiency patterns and promoting continual improvement initiatives. By examining this data, producers can determine possible areas for optimization and carry out corrective actions to improve the overall quality of their stamped products.
Enhancing Precision With Digital Equipment
Using electronic devices can considerably enhance the accuracy of steel marking procedures, changing the means makers accomplish precision in their production. Digital devices such as computer-aided layout (CAD) software application permit for the production of elaborate stamping layouts with unbelievably precise measurements. By inputting detailed requirements into the software application, producers from this source can guarantee that each stamped item meets specific dimensional needs, reducing mistakes and waste in the manufacturing procedure.
Furthermore, the combination of sensors and real-time tracking systems in stamping equipment enables makers to closely check the stamping process and make immediate modifications to make certain specific outcomes. These electronic devices provide important information on variables such as pressure, speed, and placement, allowing for quick identification and modification of any kind of discrepancies from the preferred requirements.
Conclusion
To conclude, modern steel marking approaches use various advantages for improving productivity and high quality in making procedures. By utilizing innovative modern technologies, automation, quality control steps, and digital tools, companies can boost performance, accuracy, and general performance. These technologies in metal marking not only improve manufacturing processes however also ensure constant and premium outcomes. Accepting these modern-day methods can result in considerable advancements in the production sector.